
¿Cómo optimizar la lubricación de rodamientos para prolongar su vida útil?
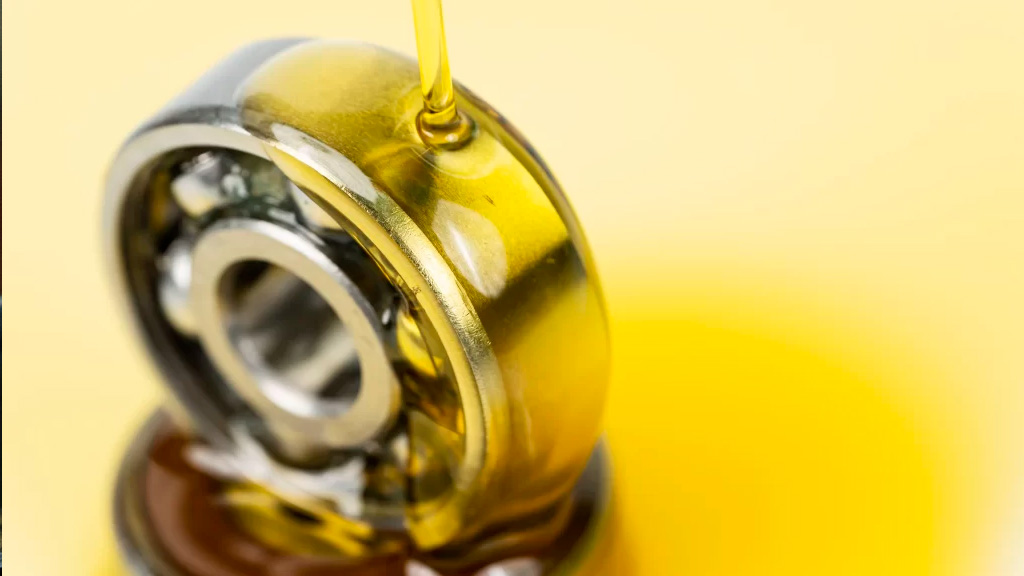
¿Qué vas a aprender en este artículo?
Importancia de la Lubricación en Rodamientos y su Impacto en la Vida Útil
La lubricación en rodamientos desempeña un papel esencial en el funcionamiento eficiente y la longevidad de estos componentes críticos en maquinaria industrial. Desde los motores de alta velocidad hasta los equipos pesados en entornos exigentes, la lubricación adecuada es un factor determinante para garantizar un rendimiento óptimo y una vida útil prolongada.
1.1 Importancia de la Lubricación en Rodamientos
La lubricación es el componente vital que permite la operación suave y eficiente de los rodamientos al reducir la fricción entre las superficies móviles. En un entorno industrial, donde las cargas y velocidades varían ampliamente, la lubricación actúa como un agente protector, formando una película delgada entre las bolas o rodillos y las pistas del rodamiento. Este efecto de separación minimiza el desgaste, la abrasión y la generación de calor, contribuyendo directamente a la confiabilidad y durabilidad del sistema.
La lubricación no solo reduce la fricción, sino que también ayuda a prevenir la corrosión al crear una barrera protectora contra la humedad y otros agentes contaminantes. Además, contribuye a la disipación eficiente del calor generado durante la operación, evitando el recalentamiento y el consiguiente deterioro de los materiales.
1.2 Impacto en la Vida Útil de los Rodamientos
La vida útil de los rodamientos está intrínsecamente ligada a la calidad y eficacia de la lubricación. Un suministro inadecuado de lubricante o la elección incorrecta del tipo de lubricante pueden acortar significativamente la vida operativa de los rodamientos. Por el contrario, una lubricación adecuada contribuye a una mayor resistencia al desgaste, una mejor capacidad de carga y una operación más suave, extendiendo la vida útil de los rodamientos y reduciendo la necesidad de mantenimiento y reemplazo frecuentes.
Además, la lubricación adecuada minimiza la posibilidad de fallas prematuras, aumentando la confiabilidad operativa de la maquinaria y reduciendo los costos asociados con tiempos de inactividad no planificados y reparaciones.
Fundamentos de la Lubricación en Rodamientos:
La lubricación en rodamientos constituye una disciplina fundamental para garantizar el rendimiento óptimo y la durabilidad de estos componentes cruciales en maquinaria industrial. Comprender los fundamentos de la lubricación es esencial para aplicar prácticas efectivas que maximicen la eficiencia operativa y prolonguen la vida útil de los rodamientos.
2.1 Rol Crítico de la Lubricación:
La lubricación desempeña un papel crítico al reducir la fricción entre las bolas o rodillos y las pistas del rodamiento. Este fenómeno de reducción de la fricción es esencial para minimizar el desgaste y la generación de calor, factores que afectan directamente la eficiencia y la longevidad de los rodamientos.
Al aplicar un lubricante adecuado, se crea una película protectora entre las superficies en movimiento, evitando el contacto directo y, por ende, la fricción excesiva. Esta película lubricante no solo facilita el desplazamiento suave de las bolas o rodillos, sino que también actúa como una barrera protectora contra la corrosión y otros agentes contaminantes presentes en el entorno operativo.
La reducción de la fricción contribuye a una operación más eficiente, minimizando la pérdida de energía por calor y garantizando un funcionamiento suave y silencioso de los rodamientos.
2.2 Funciones Específicas de la Lubricación en Rodamientos:
La lubricación en rodamientos realiza varias funciones específicas, todas ellas dirigidas a garantizar un rendimiento confiable y una vida útil prolongada:
a. Reducción de Fricción y Desgaste: La lubricación crea una película protectora que minimiza el contacto metal con metal, reduciendo así la fricción y el desgaste. Este efecto contribuye directamente a la longevidad del rodamiento.
b. Disipación de Calor: Durante la operación, se genera calor debido a la fricción. La lubricación eficaz ayuda a disipar este calor, previniendo el recalentamiento que podría afectar negativamente la integridad del rodamiento.
c. Protección contra la Corrosión: La película lubricante actúa como una barrera protectora contra la humedad y otros agentes corrosivos, ayudando a prevenir la corrosión y el desgaste prematuro.
d. Sellado y Protección: En algunos casos, la lubricación puede formar parte de sistemas sellados que protegen los rodamientos contra contaminantes externos, prolongando aún más su vida útil.

Selección del Lubricante Adecuado:
La elección del lubricante adecuado es crucial para garantizar el rendimiento óptimo y la vida útil prolongada de los rodamientos en entornos industriales. Diversos factores deben tenerse en cuenta al seleccionar el lubricante más apropiado para una aplicación específica, y conocer los tipos disponibles y sus aplicaciones facilita la toma de decisiones informadas.
3.1 Factores a Considerar al Elegir Lubricantes:
La selección del lubricante adecuado implica evaluar varios factores, adaptando la elección a las condiciones operativas específicas de cada aplicación. Algunos factores clave a considerar incluyen:
a. Carga y Velocidad: El nivel de carga y la velocidad de operación influyen en la viscosidad requerida del lubricante. Aplicaciones de alta carga o alta velocidad pueden requerir lubricantes con propiedades específicas.
b. Temperatura de Operación: La temperatura ambiente y la generada durante la operación afectan la viscosidad y estabilidad del lubricante. Es crucial seleccionar un lubricante capaz de mantener sus propiedades dentro del rango de temperaturas esperado.
c. Condiciones Ambientales: Factores como la presencia de agua, polvo o productos químicos en el entorno pueden influir en la elección del lubricante. Algunos entornos pueden requerir lubricantes resistentes al agua o con propiedades anticorrosivas.
d. Tipo de Carga: Dependiendo de si la carga es axial, radial o combinada, se pueden requerir lubricantes con aditivos específicos para hacer frente a las demandas particulares de cada tipo de carga.
e. Intervalos de Lubricación: La frecuencia con la que se puede acceder al rodamiento para la aplicación de lubricante afectará la elección del tipo de lubricante. En algunos casos, se pueden preferir lubricantes de larga duración.
f. Requisitos de Sellado: En aplicaciones selladas, la compatibilidad del lubricante con los sellos es esencial para mantener la eficacia del sellado y prevenir la entrada de contaminantes.
3.2 Tipos de Lubricantes y Sus Aplicaciones:
Existen varios tipos de lubricantes, cada uno con propiedades específicas que los hacen adecuados para diversas aplicaciones. Algunos de los tipos más comunes incluyen:
a. Grasas: Ideales para aplicaciones donde la lubricación periódica es más práctica. Las grasas ofrecen una mayor viscosidad y adherencia, siendo efectivas en condiciones de carga moderada a alta.
b. Aceites: Aplicados en forma líquida, los aceites son versátiles y se adaptan bien a aplicaciones de alta velocidad y cargas ligeras. Se utilizan comúnmente en sistemas de circulación o baño de aceite.
c. Lubricantes Secos: En entornos donde los lubricantes convencionales no son adecuados, como en presencia de polvo o alta temperatura, los lubricantes secos, como el grafito o el teflón, pueden ser una opción.
d. Lubricantes Especiales: Para aplicaciones específicas, como entornos de alta temperatura, cargas extremas o requisitos de biocompatibilidad, se pueden utilizar lubricantes especiales formulados para abordar estas condiciones particulares.
La selección del lubricante adecuado implica evaluar estos factores y elegir el tipo de lubricante que mejor se adapte a las condiciones de operación específicas de cada aplicación. Esta decisión contribuye significativamente a la eficiencia operativa y la longevidad de los rodamientos en entornos industriales.

Métodos de Lubricación en Rodamientos:
La elección entre lubricación con grasa y lubricación con aceite es una consideración crucial al diseñar y mantener sistemas de rodamientos en maquinaria industrial. Cada método tiene sus propias características y ventajas, y la elección depende de diversos factores, como la aplicación, la carga, la velocidad y los requisitos de mantenimiento.
4.1 Lubricación con Grasa:
La lubricación con grasa implica el uso de un lubricante espeso y semisólido que se introduce en el rodamiento en forma de grasa. Este método tiene varias ventajas y consideraciones:
Ventajas:
Facilidad de Aplicación: La grasa es fácil de aplicar y se mantiene en su lugar, siendo especialmente útil en aplicaciones donde la lubricación frecuente es práctica.
Sellado Efectivo: La grasa puede sellar eficientemente el rodamiento, protegiéndolo contra contaminantes y evitando la pérdida de lubricante.
Consideraciones:
Intervalos de Relubricación: La grasa tiene una vida útil limitada y puede requerir relubricación a intervalos regulares.
Temperatura: En aplicaciones de alta temperatura, la grasa puede perder consistencia y, por ende, su capacidad lubricante.
4.2 Lubricación con Aceite:
La lubricación con aceite implica el suministro continuo de aceite al rodamiento, ya sea a través de un sistema de circulación o mediante el suministro de aceite en baño. Este método tiene sus propias ventajas y consideraciones:
Ventajas:
Enfriamiento Efectivo: El aceite es eficaz para disipar el calor generado durante la operación, lo que es crucial en aplicaciones de alta velocidad o carga.
Vida Útil Prolongada: La lubricación continua puede prolongar la vida útil del rodamiento, especialmente en aplicaciones de alta exigencia.
Consideraciones:
Requerimientos de Mantenimiento: La lubricación con aceite a menudo requiere sistemas más complejos y puede necesitar mantenimiento más frecuente.
Posibilidad de Fugas: En sistemas de aceite, existe la posibilidad de fugas, lo que puede requerir sistemas de sellado adicionales.
4.3 Comparación de Métodos y Sus Ventajas:
La elección entre grasa y aceite depende de diversos factores y aplicaciones específicas. Algunas consideraciones clave en la comparación de estos métodos incluyen:
Carga y Velocidad: En aplicaciones de alta carga o velocidad, la lubricación con aceite puede ser preferible para proporcionar una refrigeración efectiva.
Sellado y Protección: La grasa es efectiva para sellar y proteger, lo que puede ser crucial en entornos donde la contaminación es un problema.
Intervalos de Mantenimiento: La grasa puede ser más práctica en aplicaciones donde los intervalos de mantenimiento son mayores, mientras que la lubricación con aceite puede ser preferible en aplicaciones de servicio continuo. En última instancia, la elección entre la lubricación con grasa y aceite dependerá de una evaluación cuidadosa de las condiciones operativas específicas y los requisitos de la aplicación para garantizar el rendimiento óptimo y la durabilidad de los rodamientos en maquinaria industrial.
También puede interesarte:
¿Te resultó útil esta información?
Ayúdanos a compartirla para que llegue a las personas que pueda serle útil.
Puedes enviarla fácilmente a través de WhatsApp.
Recuerda que compartir información es otra forma de ayudar.